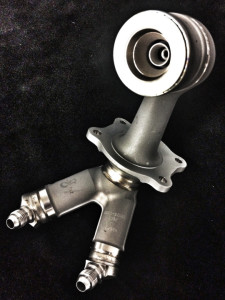
Airplanes Are Getting Lighter Thanks to 3-D-Printed Parts
Airplanes Are Getting Lighter Thanks to 3-D-Printed Parts
A rapid increase in sales of 3-D printers that make metal parts may just be the beginning of a surge in additive manufacturing in the aerospace industry.
Metal 3-D printing, which has been around for decades, is finally coming into its own as a genuine mass manufacturing technology: sales of machines that print metal objects have risen rapidly as manufacturers, especially in the aerospace industry, gear up for commercial production of additively made parts they’ve been developing for years (see “10 Breakthrough Technologies 2013: Additive Manufacturing”).
That’s according to Terry Wohlers, an industry analyst and consultant who publishes an annual volume regarded by many as the most authoritative source of analysis for the additive-manufacturing industry. Last year, companies purchased 808 machines capable of building metal parts layer by layer, up from 550 in 2014 and 353 in 2013, according to Wohlers. Annual sales growth in the hundreds of units may seem small, but these machines cost hundreds of thousands to a million dollars each.
GE has begun commercial production of this 3-D-printed fuel nozzle and eventually plans to produce 30,000 annually.
Makers of orthopedic and dental implants were among the first to begin 3-D-printing metal products; they have been producing implants this way for a few years. But the entry of the aerospace industry has the potential to turn metal additive manufacturing into a much bigger business.
Several 3-D-printed parts developed by GE, Airbus, and others are either ready for the market or close to it. In fact, GE is already using the technology to produce two complicated jet engine components—a fuel nozzle and an apparatus for housing temperature sensors—as well as parts for a turboprop engine. And companies are developing numerous additional parts for airplanes, satellites, and rockets behind the scenes.
Industrial additive manufacturing generally involves an intense heat source, either a laser or an electron beam, that melts metal powders layer by layer according to computerized instructions, building up parts as the metal solidifies. The technology is especially useful for making complicated components in relatively small volume, because developing the tools to manufacture them can be very expensive.
A container for a temperature sensor made by GE was the first 3-D-printed metal part to gain approval from the Federal Aviation Administration.
The conventional version of GE’s 3-D-printed fuel nozzle is composed of 18 individual parts that must be welded together. The new version is just a single part, and it is 25 percent lighter, which will help increase fuel efficiency. There are 19 such nozzles in a new jet engine that GE is developing, for which the company has 10,000 orders, and the company plans to use the technology to make 30,000 of these nozzles annually.
Leave a Reply